面对越来越多元化、高标准的消费者需求,汽车制造企业一直致力于科技创新和标准升级。人工智能、虚拟仿真、边缘计算、物联网……在这满满的“黑科技”背后,是对品质的永恒追求。一直以来,领克汽车围绕高质量发展理念,不断应用创新科技来激活生产潜力和完善质量体系。通过吉利工业互联网平台的赋能,领克在智能制造领域又一次实现突破,打造出一座高效率、高质量、节能环保数字化工厂。
位于成都的领克工厂总占地面积1444亩,是全球最先进的汽车生产基地之一。拥有完善的IT系统、先进的信息管理模式、一流的高精尖设备、全球统一的严苛豪华品牌制造标准等,实现了高度智能化、无人化、定制化生产,工厂年产能可达30万台。
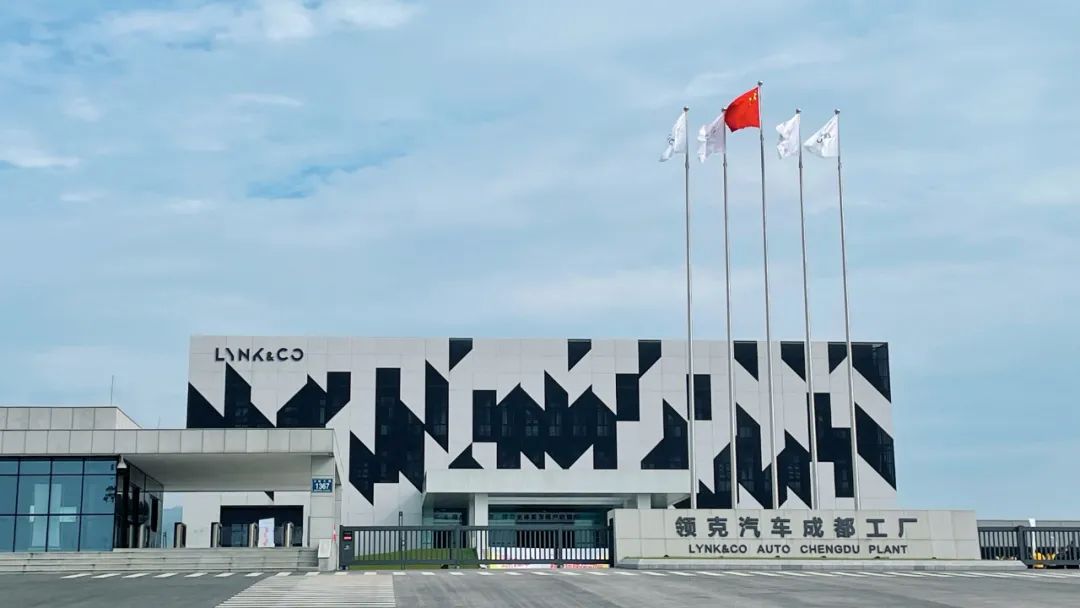
在这座大型工厂里,广域铭岛吉利工业互联网平台的智能化产品遍布冲压、焊装、涂装、总装等各大车间,为工厂构筑了坚实的数字化基础。今天,小编就带大家深入领克工厂内部,从源头揭秘数字技术在真实场景中的落地应用,近距离感受“智造”黑科技的魅力。
Geega工业物联网平台不同于市面其他IIoT平台,其核心不止连接,更多的是为机理模型全生命周期提供服务,融合OT与IT,构建模型开发、训练、验证、迭代的全流程体系,帮助企业实现数字化业务的持续优化与提升。
IIoT平台作为领克工厂数字化转型的基石,通过连接、镜像、融合、协同等特性支撑上层工业软件应用,提供即插即用的设备连接能力、数字孪生镜像能力以及产品全生命周期服务能力, 打破传统烟囱式软件架构体系, 使制造基地与供应链之间形成产业协同。
冲压智能排产:以冲压智能排产系统替代了传统的人工手动排产,担当生产调度的智脑。基于冲压排产机理模型,结合有限产能约束、DBR瓶颈、启发式算法等理论与技术,实现一键排产。
模具智能维保:自动采集冲次记录,并根据各保养类型的参数配置自动触发保养工单,并及时发现生产中的异常情况,自动派发维修工单。且与排产系统协同,将模具维修工单的处理与排产计划相联动。
容器智能管理:通过RFID技术可实时掌握容器状态,为排产系统提供数据输入,支持车间排产单批次零件生产数量达到最优,防止问题容器长期闲置。
焊接质量管理:通过焊点质量管理系统,实时获取生产过程中的海量焊点数据,基于焊接过程电热平衡和焊接参数模型应用,对每一个焊点进行质量统计与分析,对生产过程中的缺陷焊点实时预警。
焊接尺寸管理:通过尺寸管理系统整合焊装设备在线测量、蓝光测量、三坐标测量、DTS测量、内间隙测量的五维数据,基于公差传导模型,结合算法与大数据,分析尺寸失效原因。
色差管理系统:色差管理系统通过色差识别、色差预警、色差预测、色差目视评审等内容,对色差管理实现自动化、智能化、透明化和精准化,为涂装漆面外观管理提供数据支持,提升涂装外观管理质量。
缺陷识别与根因分析:利用工业视觉技术自动识别缺陷位置及类型,高效精准;结合NLP技术与联邦学习技术构建知识图谱,自动进行缺陷分析,指导工程师进行缺陷整改并沉淀为知识库,最终实现缺陷预测和规避。
对领克工厂制造全流程碳排放进行识别、监测、采集,实现企业碳盘查;建立汽车制造全生命周期碳排放评价模型和核算方法,通过碳足迹可信数字化,初步实现领克工厂的汽车碳足迹标识。
同时,针对锅炉、空压机、制冷机、循环水等共用动力版块,以IIoT平台为依托,通过机理模型、人工智能、自动控制等技术,实现能源的精准供应以降低能源成本。
OWL通过融合生产拉动、仓储、物流各自的业务特点,实现车间物料资源的柔性配送,构建生产与车间物流的一体化价值链,全面提升了工厂的执行效率和空间利用率,降低了运营成本。
仓储物流规划系统(OPS):根据生产规划、零配件数据、场地大小等,自动输出仓储物流规划方案,根据料件及节拍变化,实时优化仓储布局,动态调整物流路线。
全面仓储管理系统(OWS):将料架、容器、货物智能化,通过数字孪生,实现能力透明化,与立库、线边仓等全面打通,实现按需存储、动态储位等仓储服务。
全域物流调度系统(OLS):根据生产指令与计划,实现运输调度、搬运、分拣的无人参与和自动化,通过大量AGV机器人全面提高搬运效率,降低成本。
目前,工厂数字化解决方案除了在领克工厂实施,亦落地在湘潭基地、极氪工厂、百矿铝产业基地中,未来还将在极星基地、晋中基地、梅山基地等更多实际场景进行充分应用和验证。广域铭岛要做的是深入每个工业场景中,去发现问题、解决问题,让数据产生落地价值,真正为企业数字化转型提供动力。